Цифровизация производства в России. Как это делает ТЕХНОНИКОЛЬ
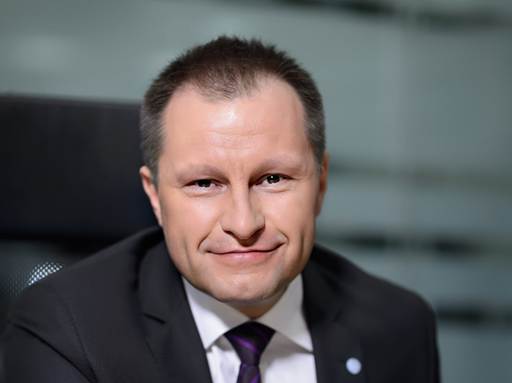
За какими ИТ-решениями охотятся крупнейшие промышленные предприятия в стране? Всегда ли они приносят реальный бизнес-эффект? Своим опытом c ECM-Journal поделился Василий Ткачев, руководитель направления «Минеральная изоляция» ТЕХНОНИКОЛЬ.
За какими ИТ-решениями охотятся крупнейшие промышленные предприятия в стране? Всегда ли они приносят реальный бизнес-эффект? И помогает ли цифровизация повысить безопасность труда на производстве? Своим опытом с ECM-Journal поделился Василий Ткачев, руководитель направления «Минеральная изоляция» ТЕХНОНИКОЛЬ.
Корпорация ТЕХНОНИКОЛЬ – международный производитель строительных материалов и систем. Одно из направлений её деятельности – выпуск теплоизоляции на основе каменной ваты.
В составе компании 8 заводов в России. Предприятия выпускают минеральный утеплитель для частного, индустриального и промышленно-гражданского строительства, техническую изоляцию и огнезащиту, а также материалы для судостроения и сельского хозяйства.
– Василий, какие технологии и решения актуальны для вашей компании сегодня?
– Цифровизация производства, автоматизация технологических линий и внедрение искусственного интеллекта, направленного в том числе на улучшение контроля качества продукции. Именно такие проекты ведутся на всех предприятиях компании.
Автоматизация бизнес-процессов и использование информационных систем, в частности в логистике, позволили за 8 лет увеличить производительность труда на 113%, повысить уровень сервиса до 90-95% и сократить сроки отгрузки готовой продукции на 45%. |
– А какие процессы перевели в цифру в первую очередь?
– Прежде всего, в электронный вид мы перевели обслуживающие процессы и собственные внутренние услуги, которые есть у любой промышленной компании вокруг центрального производства. К ним относятся логистика, планирование, цифровое проектирование BIM, онлайн-обучение.
Компания полностью перешла на электронный документооборот (ЭДО), что с учётом пандемии стало особенно актуальным.
До перехода на ЭДО много проблем возникало с бумажными документами: опаздывала их доставка, сложно было исправлять ошибки, росли расходы на курьерские и почтовые службы, тратилось лишнее время на перемещение договоров внутри организации, появлялись налоговые риски и ограничения при проведении тендеров. С переходом на ЭДО эти проблемы исчезли. |
Также стало возможным составлять договор в электронном виде с участием нескольких сторон. Такой документ в программе представляется набором определённых параметров: информация о контрагентах (адреса, названия, организационно-правовая форма), стоимость услуг, предмет и условия и т.д., после чего составление контракта идёт по автоматической логике. Программа может проанализировать надёжность подрядчика всего за несколько секунд, в то время как человеку понадобилось продолжительное время на изучение судебной практики, статистики, оценку выручки и т.д. Теперь же сотрудник только вносит данные и на выходе получает готовый документ.
Цифровизация применяется и в планировании производственного процесса. При согласовании заказа с клиентом информационная система оперативно анализирует загрузку технологических линий и определяет дату производства, а затем – автоматически ставит заказ в план работ.
Следующий этап промышленной цифровизации происходит после отгрузки продукции на склад, где она размещается с помощью системы управления складом (WMS). В дальнейшем при формировании заказа для отправки клиенту сотрудники видят в системе WMS местонахождение нужного материала. Эта же система контролирует правильность отгрузки товара, проверяя отсканированные специалистом идентификационные коды маркировки.
Эффективность работы после внедрения WMS значительно повысилась: срок нахождения транспорта на заводе сократился на 7%, а производительность труда на складе выросла на 10%. |
– Цифровизация – один из приоритетов промышленности. Так ли это для вас?
– Да, хотя целью компании была не только цифровизация, но и цифровая гибкость. Она увеличивает скорость принятия решений, что особенно ценно в условиях быстро меняющегося рынка и нестабильного спроса.
Цифровая гибкость подразумевает управление территориально распределенными активами, умение быстро перепланировать загрузку мощностей и оперативно изменять цены. |
В этом нам помогает инструмент диспетчеризации: он распределяет заявки в едином центре, объединяющем несколько предприятий. В итоге исключается ситуация, когда клиент ждёт продукт больше положенного времени из-за того, что завод не справляется с потоком заказов, а получает его в срок по той же цене, но с другого производства.
Кроме того, цифровизация практически любого бизнеса – тренд последнего времени. Тот, кто не успеет вовремя перейти на «цифровые рельсы», рискует в какой-то момент оказаться аутсайдером. |
Так, смежные с нами отрасли, такие как проектирование и архитектура, сейчас тоже активно направляются в эту сторону: двухмерное пространство превращается в трёхмерное, проекты создаются в 3D-моделях. Поэтому не только в России, но и в странах Евросоюза мы делаем упор на то, чтобы перевести решения из плоских моделей в BIM-технологии. Они позволяют спроектировать здание и ещё до начала строительства полностью просчитать и определить все процессы, которые будут в нём происходить. Использование BIM даёт возможность принимать правильные решения на всех стадиях жизненного цикла зданий и сооружений: от концепций и инвестиций до эксплуатации и даже обеспечения сноса. А если говорить о стоимости полного строительного цикла, то обеспечивает экономию в десятки процентов.
– Какие основные преимущества вы видите в новых технологиях на производстве? Можете ли расписать их на своём примере?
– Во-первых, цифровизация помогает нам улучшить качество и скорость принятия решений. Благодаря ей глубина, детализация и быстрота получения информации повышаются во много раз. Это позволяет принимать решения на более ранних стадиях и увеличивает их гибкость.
Если раньше для сбора и анализа данных о работе линии нам требовалось 12 часов, то сегодня это происходит каждые 30 секунд. Мы одновременно видим параметры готовой продукции, производственного процесса и состояния оборудования. То есть фактически в любой момент времени понимаем качественные характеристики выпускаемой продукции, знаем, на каком сырье работаем и что в данный момент происходит с оборудованием. |
Во-вторых, мы смогли исключить циклические стандартные операции. Программа чётче и быстрее человека делает такую работу, а сотрудники получают шанс заняться более ответственными и интеллектуальными задачами. С этим помогает справиться система MES (Manufacturing Execution System). Чтобы проверить качество продукции, начальник смены вносит в программу характеристики выпущенного материала. Затем она без вмешательства человека сравнивает их с эталонными показателями и формирует отчёт с замечаниями, если таковые имеются. Это значительно оперативнее, чем отправлять образцы материала в лабораторию и проводить их исследование там. А кроме того, позволяет освободившемуся лаборанту заняться другими, возможно более интересными и креативными проектами.
В-третьих, теперь мы быстро получаем данные там, где человек без помощи техники просто не может с той же скоростью находить и просчитывать причинно-следственные связи. Цифровые технологии их отслеживают и информируют, когда нужно вмешаться.
Так, машинное зрение участвует в оценке качества продукции. Если меняется один из параметров производства (качество сырья, показатели оборудования, скорость выпуска и т.п.), программа делает вывод и об изменении готового продукта и проинформирует об этом. Это, с одной стороны, позволяет быстро справляться с неполадками, а с другой – сокращать издержки. |
В-четвертых, благодаря прикладным цифровым технологиям мы повысили уровень безопасности труда. Сейчас на предприятии в Ростовской области автоматически контролируется нахождение сотрудников в каске (обязательное требование для нашего производства), а также при появлении человека в запретных зонах отключается там оборудование.
Общим итогом внедрения цифровых технологий, принципов бережливого производства и регулярно проводимых улучшений для нас стало ежегодное наращивание по 200 дополнительных часов работы оборудования. Производительность труда в среднем по компании составляет 18,7 млн руб. на человека, а на некоторых заводах превышает 45 млн рублей на каждого сотрудника.
Комментарии 0